Look down on the engine to figure out which. All engines leak somewhat so even on a healthy engine the gauge will drop down to 90 psi 10 leakage or so.
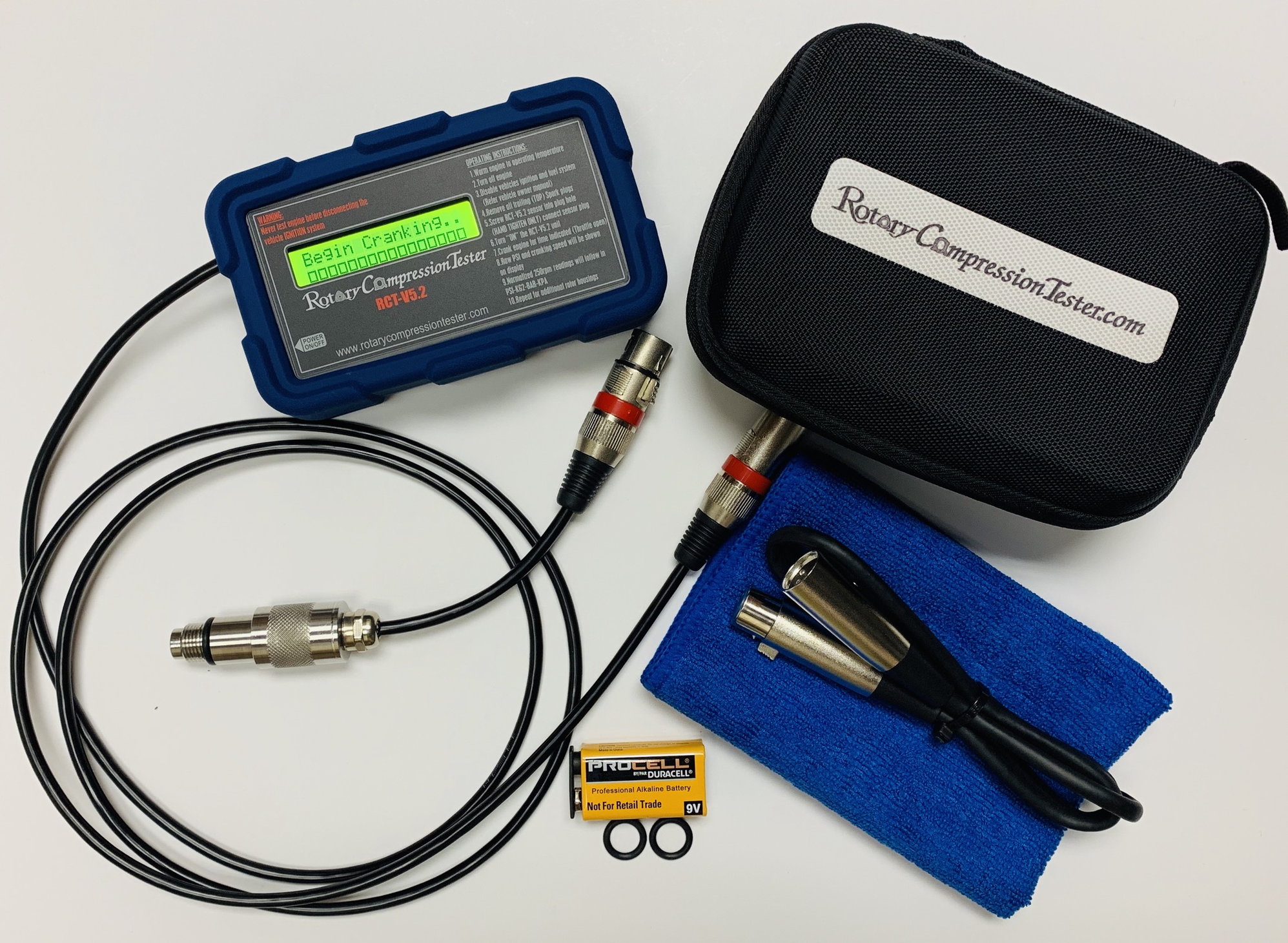
Diy Build Your Own Automated Rotary Compression Tester For
How to make a compression tester. You will be able to hear the cranking speed slow. If the hose does not fit check the hardware store for a. Compressed air 80 to 90 psi is then fed into the cylinder. How to make a pressure test fitting from a spark plug for compression testing or leak down testing. As the tested cylinder comes up on its compression stroke. Performing the test 1.
If youre testing a diesel engine make sure youre. The crankshaft is then turned so that each piston is at top dead centre. How to make a compression test gauge. First of all connect the tester to a cylinder and turn the engine over 6 to 8 compression strokes. Crank the engine at least 4 times to. Connect the compression gauge to the opposite end of the hose.
A threaded coupling is screwed into a spark plug hole. Most people start with cylinder number one and follow the engines firing order. It seems to work pretty good. Using a few air fittings i made an adapter to convert a compression tester into a cylinder leak down tester. Compression tester turned leak down tester duration. Note how fast the compression increases and write down the highest reading.
Take the compression gauge and screw it onto one end of the hydraulic hose. Take an old spark plug to the hardware store and locate a male coupling that is the same size as the spark. Make sure the cylinder is at tdc of the compression stroke so all the valves are closed and attach the leakdown tester to the cylinder head. If it drops a large amount then you have a leak from chipped valves or a bad headgasket etc. Thanks everyone for watching. Put the compression test adapter into the engines first cylinder.